Reviving scented silk quilts from the Nawabi era – GetBengal story
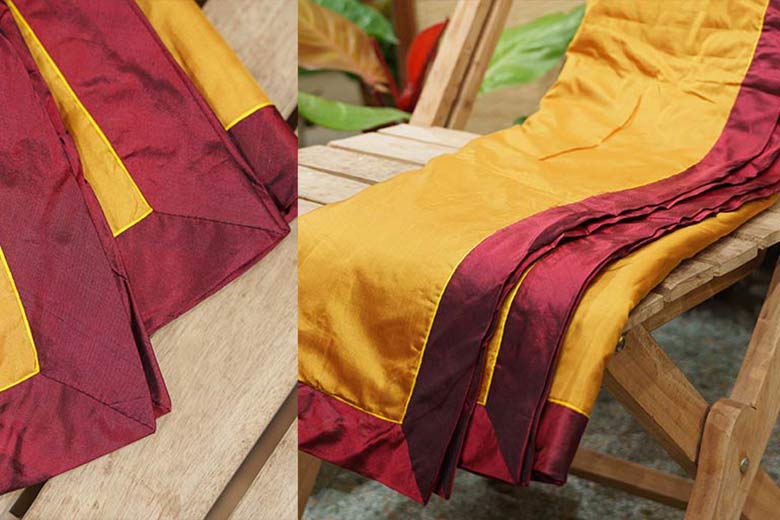
Late autumn heralds the arrival of winter in Bengal; dew gathers on the blades of grass; mist darkens the morning; and as icy wind from the north blows and penetrates the land, homemakers take out mothball-scented woollens and quilts from cupboards to protect themselves from the cruel sting of winter. These quilts are a part of Bengal's heritage.
The process of making the balaposh is quite complicated and involves multiple stages of layering and stitching, and then adding the essential oil, attar, within the layers to make it fragrant. The ‘Balaposh’ (quilt) originated in Murshidabad, the capital of Bengal Subah, in the 18th century. According to legend, Nawab Shuja-ud-Din Muhammad Khan, the reigning monarch of Bengal and the heir apparent to Nawab Murshed Kuli Khan, was dissatisfied with the traditional animal-hair (wool) blankets. He wanted something that would be “soft like a mother's lap, warm and comfortable, yet light like a beloved’s embrace and fragrant like a flower.”
Rising up to this challenge, a local artisan named Atir Khan worked on the concept for months until he hit upon the idea of creating the ‘Balaposh,’ which would be something unique and completely different from the traditional Kantha, Razai, or Dohar. Sometime between 1727 and 1739, the Balaposh was finally created. According to another popular version, the ‘Balaposh’ was invented during the reign of Nawab Siraj-ud-Daulah, who ascended to the throne 17 years after Nawab Shuja-ud-Din Muhammad Khan’s demise.
The knowledge of the production process and the skills required for making balaposh were carefully guarded family secrets passed down through generations of Atir Khan’s descendants. Until a few years ago, Sakhawat Hussain Khan, the great-grandson of Atir Khan and a resident of Khagra Chowrasta, near Bara Masjid, Murshidabad, was the only master artisan in the land who could create a perfect ‘Balaposh’, the kind used by Nawabs and the nobility. After his demise, his two daughters and a son are proudly carrying on the mantle of their family’s heirloom.
Sakhawat Hussain Khan's eldest daughter, Bobby, said that her father learned the technique from his father, a very accomplished artist who was also knowledgeable in a variety of other handicrafts, and that their family has been involved in it for many generations. She reminisced about how she and her siblings watched, fascinated by her grandfather’s skills. The three siblings picked up the business from their father. It was bewitching for them to see how their father carefully weaved one after another Balaposh adroitly, making the process look very simple. However, reality is far from that. The creative process requires the artisan to alienate himself totally from the humdrum of life and focus on his work completely. It is like a sadhana (austere ascetic practice). Any distraction or lack of concentration can mar the entire creative process. Throughout the making of the balaposh, the craftsman shuts himself up in a closed room, where not even the slightest sound of water can enter to distract him.
Balaposh is made with carded cotton. Carded cotton is cotton that has been prepared for spinning into thread or yarn. Carding is an important step in the process of making textiles to ensure that debris is removed while aligning the fibres to make them easier to spin. Without carding, cotton thread would be coarse and extremely fragile. Artisans themselves handpick the best-quality cotton, which they then refine over time. First, the work of 'bhunai' begins by cutting this cotton by hand. For 'bhunai' there is a special type of machine, with the help of which the cotton is cleaned 20 to 25 times. With each step, the cotton becomes fluffier and lighter. This process alone takes five to six days. Some of this quilt’s distinguishing features are that the fine cotton filling does not become lumpy with use and age and that all the layers that constitute it are held together only by stitches along the edges.
The process of making the quilt involves multiple stages of layering and stitching. Fine silk fabric is first laid on the floor, over which the second layer of carded cotton fibre, perfumed with the essential oil attar, is added. Then, the third layer of malmal fabric and the fourth layer of silk are subsequently overlaid, covering the cotton completely. Widely spaced stitches are then made along one edge of all four layers, holding them together. The fifth layer of silk is added, and the quilt is stitched again using broad silk ribbons of contrasting colours along all four edges. Finally, the attar is once again applied by hand to the finished quilt, which is then folded—scented side inwards—and packed into a box. Firdous Attar is most in demand. However, Rooh-Gulab Attar is also used on special occasions. The fragrance has remained ensconced within the balaposh for decades.
Working from scratch, including bhunai, layering and stitching, packing, and marketing, Bobby and her siblings work in tandem. The production technique is vastly different from that of the commercialised variety. How the three layers (a thin sheet of attar-scented cotton snuggled between two blankets of silk) should be laid is still a mystery to the rest of the world, but to the descendants of Atir Khan’s family. Despite rising demand in the market for their handcrafted, unique Balaposh, the siblings cannot always rise up to the challenge, largely due to a lack of capital.
Renowned for their royal roots, clever construction, and unique designs, these scented quilts represent the corps d'elite of Bengali handiwork. Once considered a status symbol, their demand began to dwindle with a decrease in patronage. The introduction of a market economy and the subsequent arrival of commercially produced balaposh have led to a decline in handmade balaposh. Despite this, connoisseurs of art from around the world flock to them to buy and preserve these outstanding works of art.
In addition, the authorities of the local Anukul Thakur’s ashram buy a pristine white balaposh annually. The Bengal Store has just launched the high-quality traditional balaposh. In the reign of the Mughal Nawabs, high-quality corpus cotton was used to make balaposh quilts. Pure corpus cotton is unadulterated or free from any impurities or mixtures. It specifically denotes cotton fibres that are in their natural state, without any synthetic or artificial additives.
The Bengal Store has restored the corpus cotton and silk wrap Balaposh of the erstwhile Nawabs.
Address: 127, Jodhpur Park, Kolkata 700068 (open from Sunday to Tuesday).