Banak – Colour of Bengal’s Clay Art
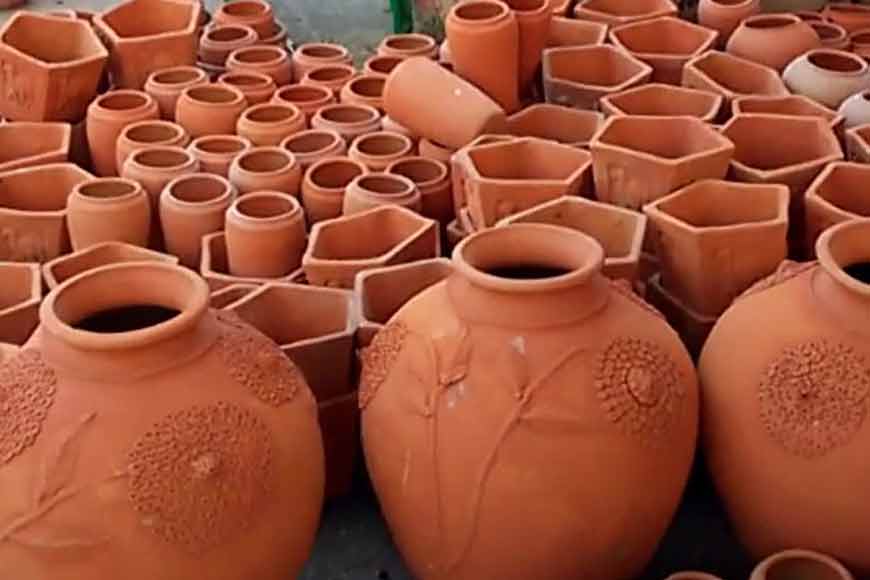
There was a time when the artists and artisans of Bengal used a variety of colours produced in a traditional format on their objects of art to make them look more attractive. These colours were derived from natural and mineral resources and their production process was quite arduous. With the introduction of chemical paints many of these systems and procedures of making colours vanished. Yet the potters’ community of Bengal has still preserved some age-old traditional colour making. Take for example the red colour on their pots and vases is originally a muddy yellow that turns red after burning. In scientific terms, it can be said that this colour which is a combination of silica and iron derived from sand grains becomes reddish when placed under fire. The method by which this indigenous colour is collected by artists is also quite unusual.
After making the earthen pots and pitchers, the potters allow them to dry out for some time before applying a coat of yellow colour on their outer surface, which is known as banak. When these earthen wares are burnt in specially built kilns, known as pone, it is seen that the surface painted with banak has turned bright red. The brightness of this red varies from place to place and in the hands of different potters, as it is largely dependent on the use of good quality soil and on the perfection of the production process.
The name Banak has been derived from the word Barnak, which literally means anything to coat or smear with. This colour is generally found below the ground in areas around the potters’ dwellings. But considerable experience is needed to correctly identify this colour as it lies hidden under the earth. While the potters’ groups living in different parts of West Bengal have their own methods for gathering this colour locally, several small units have been set up in various places for the extraction of banak, notable among which is the Chandrakona Unit of Medinipur District. The coloured soil is gathered by digging inclined holes ten to fifteen feet deep, each in selected areas around the above villages having red, uneven, gravel soil, in which the rainwater runs down as rapids during monsoons.
Several Banak production units are in Garbeta and Tamluk as well. The soil collected from the holes is first dried up thoroughly and then allowed to soak in water in a shallow hole or cistern for several days. When the soil is properly soaked, more water is added as per requirement and then it is trampled upon with feet. Once the clay containing sand and gravel gets settled at the bottom, the fluid portion is taken out from the top in small earthen pots and allowed to dry in the sun. When the fluid collected in the earthen pots dries up, the sediment left in the bottom is taken out and it is this which serves as Banak.
The producers stack this muddy material for sale. While local artisans have easy access to this ingredient, many purchasers arrive from Kolkata and Baharampur for collecting it from the producers. Nowadays there is an increasing demand for earthen tiles for roof covering, these tiles are soaked in Banak before they are burnt in the fire to enhance the brightness of their red colour. This has led to a good demand for Banak colours. The artisans mix the banak with water as required for preparing the paint, which they then apply on earthen vessels with mops or brushes. Great care is taken about the source of water used for mixing the Banak. If the water used is from any pond or tubewell, the resulting colour after burning does not turn out to be bright red. So the potters prefer to use only rainwater for the task. And for this reason, they use all available vessels for storing rainwater during the monsoon.
The application of Banak on a soft clay surface brings out a reddish colour after burning. But apart from the red-coloured vessels, the potters also make earthen vessels of black colour, which are used for various domestic purposes. For instance, small earthen pots of black colour known as donis were extensively used at one time for storing ghee or oil. The black pitcher used nowadays for storing drinking water is also another example of such an earthenware.
Even though there is a gradual decline in the use of such vessels, the potters' community of Medinipur, Howrah and Bankura districts still produce these.
(Data source: Folk Arts of West Bengal and the Artist Community)